Introduction
Robots in Industry:
The advent of robotics has significantly transformed various industries worldwide. From manufacturing to logistics, robots are increasingly being deployed to automate tasks, enhance efficiency, and reduce operational costs. Companies are leveraging advanced robotic technologies to optimize production lines, improve quality control, and create safer work environments. This article delves into the role of robots in industrial settings, exploring how they drive efficiency and cost reduction while shaping the future of work.
The Evolution of Industrial Robotics
Industrial robots have come a long way since their inception in the mid-20th century. Initially, these machines were primarily used for simple, repetitive tasks such as assembling car parts in the automotive industry. Today, advancements in artificial intelligence (AI), machine learning, and sensor technology have enabled robots to perform complex tasks with high precision. Modern robots can analyze data, adapt to changing environments, and collaborate with human workers, making them indispensable in various sectors.
The evolution of robotics has been driven by the need for increased productivity and competitiveness. Early adopters of robotic automation, such as automotive and electronics manufacturers, have set the stage for widespread adoption across different industries, including healthcare, food processing, and logistics.
Increasing Efficiency with Robotics
One of the primary benefits of industrial robots is their ability to enhance efficiency. Unlike human workers, robots can operate 24/7 without breaks, fatigue, or errors, ensuring continuous production and higher output levels. Some key ways in which robots improve efficiency include:
- Speed and Precision: Robots perform tasks faster and with greater accuracy than human workers. This is particularly beneficial in assembly lines, where high-speed production is crucial.
- Automation of Repetitive Tasks: Robots handle monotonous and physically demanding tasks, freeing human workers to focus on higher-value activities such as quality control and innovation.
- Improved Quality Control: With advanced sensors and AI-driven analytics, robots can detect defects and inconsistencies in real time, reducing waste and ensuring product quality.
- Data-Driven Optimization: Smart robots equipped with IoT (Internet of Things) capabilities collect and analyze data to identify inefficiencies and suggest process improvements.
- Scalability: Automated systems allow companies to scale operations quickly in response to market demands without significantly increasing labor costs.
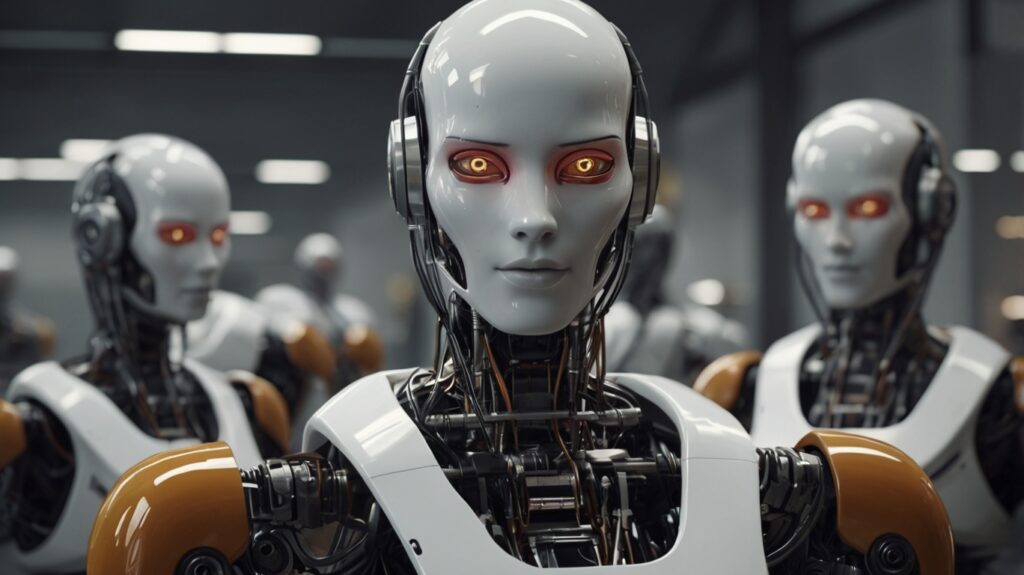
Reducing Costs Through Robotics
Cost reduction is another significant advantage of integrating robots into industrial processes. Although the initial investment in robotic systems can be substantial, the long-term savings outweigh the costs. Here’s how robots contribute to cost reduction:
- Lower Labor Costs: Robots minimize reliance on human labor for repetitive and hazardous tasks, reducing wage expenses and related costs such as benefits and insurance.
- Energy Efficiency: Modern robots are designed to consume less energy than traditional machinery, leading to lower electricity bills and a smaller carbon footprint.
- Reduced Material Waste: Precision in robotic operations minimizes material wastage, cutting down on raw material costs and environmental impact.
- Decreased Downtime: Unlike human workers who require rest periods, robots can operate continuously with minimal maintenance, ensuring maximum uptime and productivity.
- Fewer Workplace Accidents: By taking over dangerous tasks, robots reduce workplace injuries, leading to lower compensation claims and medical expenses.
Case Studies: Industries Benefiting from Robotics
Automotive Industry
The automotive sector was one of the first industries to adopt robotics extensively. Companies like Tesla and Toyota utilize robotic arms for assembling vehicles with remarkable speed and precision. These robots handle everything from welding and painting to quality inspections, significantly improving production efficiency and consistency.
Logistics and Warehousing
E-commerce giants such as Amazon and Alibaba rely on robotic automation for inventory management and order fulfillment. Automated guided vehicles (AGVs) and robotic arms streamline warehouse operations by picking, sorting, and packing goods, reducing processing times and operational costs.
Healthcare and Pharmaceuticals
In the healthcare sector, robots assist in surgeries, laboratory testing, and pharmaceutical manufacturing. Robotic-assisted surgery, for instance, enables minimally invasive procedures with greater precision, reducing recovery times for patients and hospital costs.
Food and Beverage Industry
Food processing plants employ robots for packaging, labeling, and quality control. Automated systems ensure hygiene and consistency in food production while reducing labor costs and minimizing food waste.
The Human-Robot Collaboration
While robots are enhancing efficiency and reducing costs, they are not necessarily replacing human workers. Instead, they are transforming job roles and creating new opportunities. Collaborative robots, or cobots, are designed to work alongside humans, assisting with tasks that require dexterity and adaptability.
Companies are investing in workforce training programs to equip employees with the skills needed to operate and maintain robotic systems. This shift from manual labor to robotic supervision and programming is helping industries stay competitive in an increasingly automated world.
Challenges and Considerations
Despite the numerous benefits, integrating robots into industrial processes comes with challenges:
- High Initial Investment: The upfront cost of purchasing and implementing robotic systems can be a barrier for small and medium-sized enterprises (SMEs).
- Technical Complexity: Maintaining and programming robots require specialized knowledge, necessitating continuous training for employees.
- Cybersecurity Risks: As robots become more interconnected, they are vulnerable to cyber threats, requiring robust security measures to protect industrial data.
- Ethical and Workforce Concerns: The rise of automation has sparked debates about job displacement and the future of employment. Industries must balance automation with workforce development to ensure economic sustainability.
The Future of Industrial Robotics
The future of industrial robotics is promising, with continuous advancements in AI, machine learning, and robotics technology. Some emerging trends include:
- AI-Powered Robotics: Robots will become smarter and more autonomous, capable of making real-time decisions and learning from their environments.
- Cloud Robotics: Connecting robots to the cloud will enable remote monitoring, predictive maintenance, and seamless software updates.
- Humanoid Robots: Industries may see increased adoption of humanoid robots for customer service and specialized tasks requiring human-like interactions.
- Green Robotics: Eco-friendly robots designed with sustainable materials and energy-efficient technologies will contribute to environmental conservation efforts.
Conclusion
Robots are revolutionizing industries by increasing efficiency, reducing costs, and enhancing overall productivity. While challenges remain, the benefits of automation far outweigh the drawbacks. As technology continues to evolve, industries must embrace robotic solutions to stay competitive in an increasingly digital world. By fostering human-robot collaboration and investing in workforce upskilling, businesses can unlock the full potential of automation and drive sustainable growth in the industrial landscape.
Robots in Industry:
Frequently Asked Questions (FAQ) on Industrial Robotics
1. What are industrial robots?
Industrial robots are automated machines used in manufacturing and other industries to perform tasks such as assembly, welding, painting, quality control, and packaging. These robots help improve efficiency, reduce costs, and enhance workplace safety.
2. How have industrial robots evolved over time?
Industrial robots have advanced significantly since their introduction in the mid-20th century. Initially used for simple repetitive tasks, modern robots are now equipped with artificial intelligence (AI), machine learning, and advanced sensors, allowing them to perform complex tasks, adapt to changes, and collaborate with human workers.
3. What industries benefit the most from robotics?
Several industries benefit from robotics, including:
- Automotive: Robots assist in assembling vehicles, welding, and painting.
- Logistics and Warehousing: Automated systems streamline inventory management and order fulfillment.
- Healthcare and Pharmaceuticals: Robots aid in surgeries, laboratory testing, and pharmaceutical production.
- Food and Beverage: Robots enhance packaging, labeling, and quality control processes.
4. How do robots improve efficiency in industrial settings?
Robots enhance efficiency by:
- Operating 24/7 without fatigue.
- Performing tasks with high speed and precision.
- Automating repetitive and physically demanding jobs.
- Utilizing AI and IoT to optimize processes and reduce waste.
5. How do robots help reduce operational costs?
Robots contribute to cost reduction by:
- Lowering labor costs by handling repetitive and hazardous tasks.
- Increasing energy efficiency compared to traditional machinery.
- Minimizing material waste through precision operations.
- Reducing workplace accidents and associated medical expenses.
6. Are robots replacing human workers?
Rather than replacing human workers, robots are transforming job roles. Many industries now use collaborative robots (cobots) that work alongside humans, enhancing productivity and safety. Companies are also investing in workforce training programs to help employees adapt to robotic technology.
7. What are the challenges of implementing industrial robotics?
Some challenges include:
- High initial investment costs, particularly for small businesses.
- Technical complexity requiring specialized knowledge and training.
- Cybersecurity risks as interconnected robots become targets for cyber threats.
- Ethical and workforce concerns related to automation and job displacement.
8. What are some emerging trends in industrial robotics?
Future trends in industrial robotics include:
- AI-powered robotics that enable real-time decision-making and adaptability.
- Cloud robotics for remote monitoring and predictive maintenance.
- Humanoid robots for customer service and specialized interactions.
- Green robotics with sustainable materials and energy-efficient technology.
9. How can businesses integrate robotics effectively?
To successfully integrate robotics, businesses should:
- Conduct a cost-benefit analysis before investing in automation.
- Provide training programs to help employees work alongside robots.
- Implement cybersecurity measures to protect robotic systems.
- Continuously monitor and upgrade robotic solutions for maximum efficiency.
10. What is the future of industrial robotics?
The future of industrial robotics is driven by advancements in AI, machine learning, and automation. As robots become more intelligent and autonomous, industries will continue to adopt innovative robotic solutions to improve productivity, safety, and sustainability in the workplace.